Success story
STELLANTIS
Restore your CMM’s peak performance and maximize its life with a software retrofit
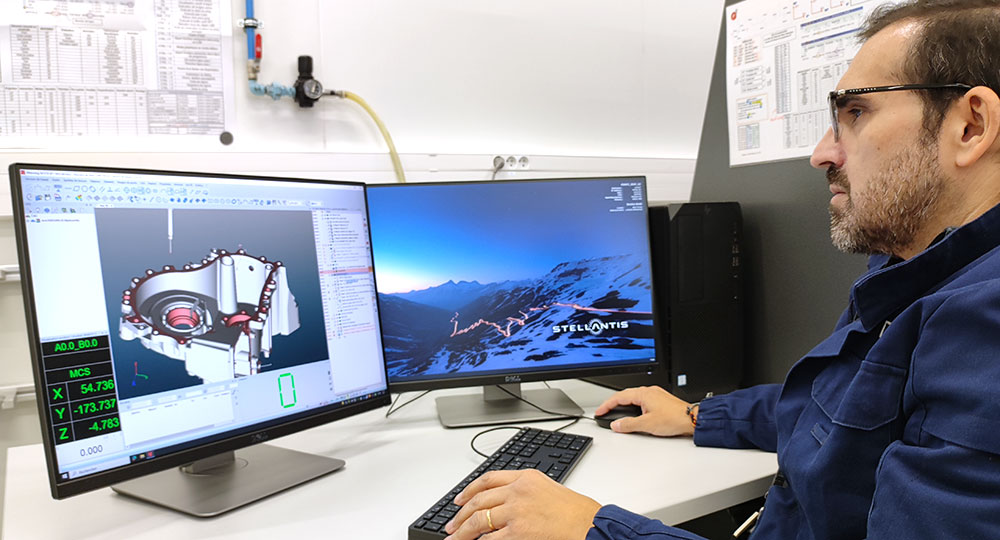
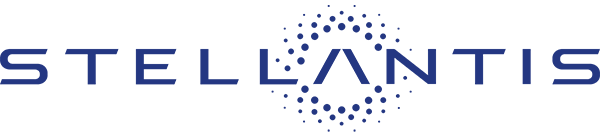
Stellantis is a global automotive manufacturer resulting from the merger between the PSA Group and FCA in 2021, which today markets fourteen automotive brands worldwide.
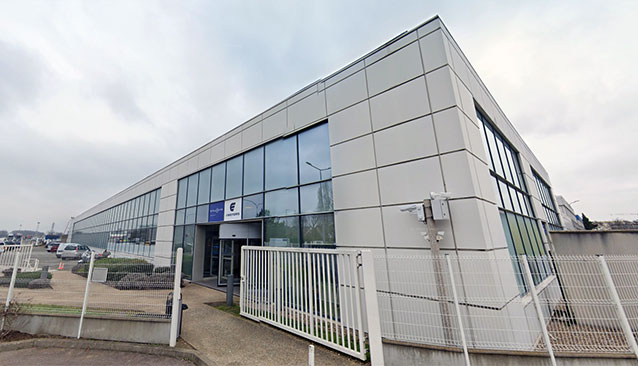
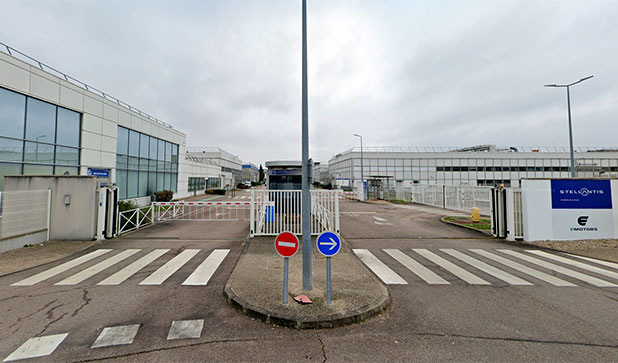
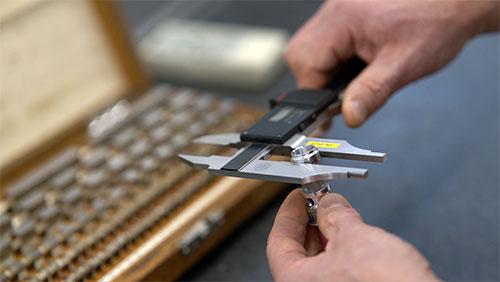
The Stellantis metrology laboratory is accredited to A109000, the reference standard for Stellantis laboratories (based on ISO 17025). “For over 30 years, our laboratory has been at the service of the design of all automotive mechanical components, and is therefore very involved in mechanical functions” explains Jean-Pierre HUGUET, Metrology Manager. The metrology department’s know-how is applied to all parts requiring precision, including internal combustion and electric motors, transmissions, chassis, as well as mechanical and electrical parts, all of which require adapted measurement methodologies. “Here, each part measurement requires specific expertise and the creation of a customized program” explains Olivier LASSALLE, metrology technician. The site uses four CMMs (three-dimensional measuring machines): DEA, Wenzel, Leitz 864 and Leitz 866.
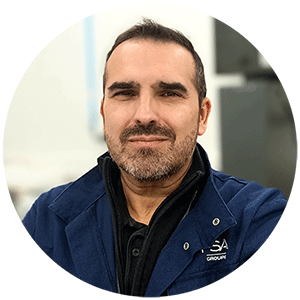
José FERNANDEZ
3D Support Technician
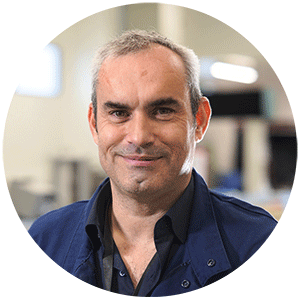
Jean-Pierre HUGUET
Metrology Manager
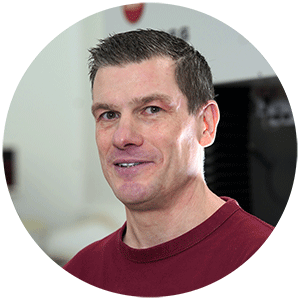
Olivier LASSALLE
Metrology Technician
What to do with an aging CMM?
Despite the accuracy that is crucial to ensuring product quality, a CMM may be aging and starting to pose major challenges in terms of ongoing support and reliability. In such cases, a software retrofit is an advantageous solution for modernizing measuring equipment.
“Our two Leitz CMMs have been in use for 35 years, and thanks to their fixed head, scanning accuracy and ability to integrate a rotary table, they remain valuable assets for our laboratory,” says José FERNANDEZ, 3D support technician. “However, these CMMs were equipped with old and complex software which the metrology technician had not been able to use completely independently, and which no longer complied with the ISO GPS standard.”
Faced with this situation, the metrology department wondered:
- Should we invest in new CMMs and give up these two Leitz CMMs?
- Should we keep these two CMMs and invest in new training courses on the existing software?
- Should the existing software be replaced by new software?
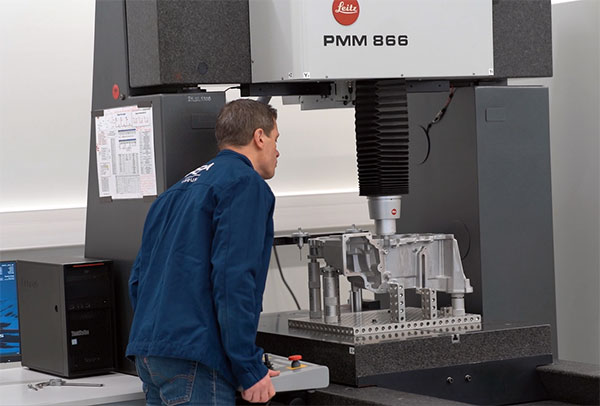
-
Extend the life of a CMM by restoring full performance at lower cost than buying a CMM
The metrology department made the decision to extend the life of the Leitz CMMs: replace the existing software with Metrolog X4. “This upgrade has brought our equipment back to life, enabling us to maintain optimum performance without investing in new machines,” notes Jean-Pierre HUGUET. The Metrolog X4 software has improved the overall performance of the CMMs, making them easier to program, without compromising on the accuracy of results.
With a more intuitive, user-friendly interface, Metrolog X4 has won over users. “What I particularly appreciate about Metrolog X4 is its user-friendly interface, visual clarity and programming comfort”, says Olivier LASSALLE.
This low-cost alternative has enabled us to achieve a real return on investment by avoiding the purchase of new CMMs. “In addition to the gains in performance and efficiency, this solution avoided the need for a major investment in new CMMs, which would have entailed purchasing, installation and technician training costs,” asserts José FERNANDEZ.
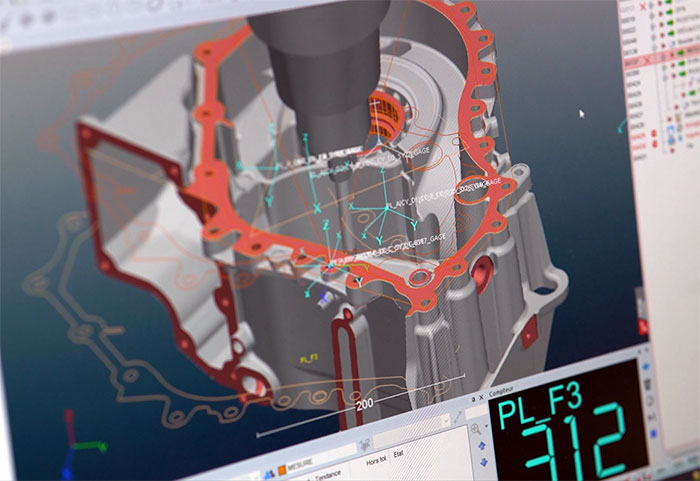
-
Meet the latest standards and be ready for the future with a scalable solution
In the context of evolving standards, it is necessary for the metrology laboratory to remain compatible with, among others, the ISO GPS (Geometrical Product Specifications) standard to maintain its activity. This standard is essential for standardizing the geometrical specifications of parts, enabling consistent interpretation of tolerances on the drawing. It ensures that each component meets the precision criteria required to guarantee its assembly and functionality within an assembly.
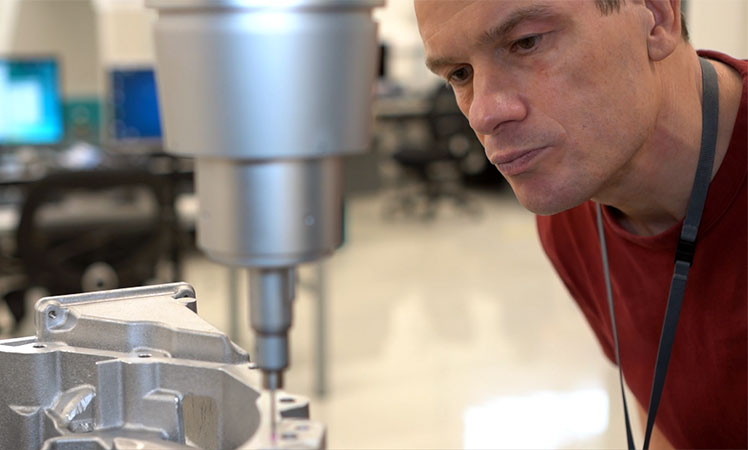
“I was first trained in-house on Leitz machines, using obsolete and aging software that no longer complied with the ISO GPS standard. Training on this software was not enough to enable me to achieve complete autonomy,” notes Olivier LASSALLE.
Adopting a recent and upgradable software such as Metrolog X4 has enabled the laboratory to obtain measurement software that complies with the latest standards. “Importing CAD files and managing geometric tolerances according to ISO standards make the software very practical for complex measurements,” explains Olivier LASSALLE.
-
Benefit from a single software solution for all CMMs
A fleet of machines, each equipped with a different software package, requires resources capable of mastering several different software packages, which was becoming complicated at Stellantis. The issue of internal skills management prompted the metrology team to question the relevance of keeping the two Leitz CMMs, which were equipped with their original software.
One of the major advantages of this retrofit project lies in the use of a single, universal software package for all the laboratory’s CMMs, whatever their model or application. “This simplifies our day-to-day work and reduces the need for specific training for each machine, making our team more versatile and efficient,” notes Jean-Pierre HUGUET.
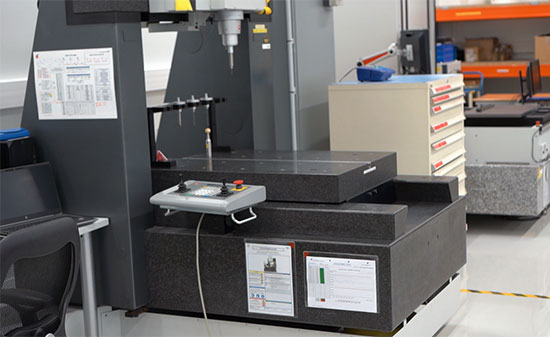
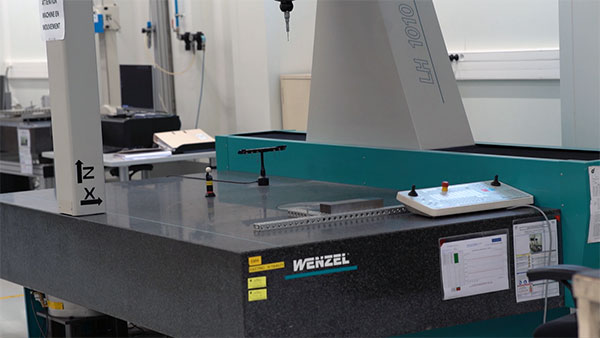
What’s more, the laboratory’s other two CMMs were already equipped with Metrolog X4. “All our technicians have mastered Metrolog X4, which simplifies the use of these machines and enables us to take full advantage of their capabilities,” notes José FERNANDEZ. Olivier LASSALLE underlines the importance of collaboration within his team for the transfer of knowledge: “Thanks to this new software and additional training, I am now able to use it independently, and I have been able to count on the support of my colleagues, who have also mastered Metrolog X4”.
In conclusion: retrofitting to extend CMM life without compromise
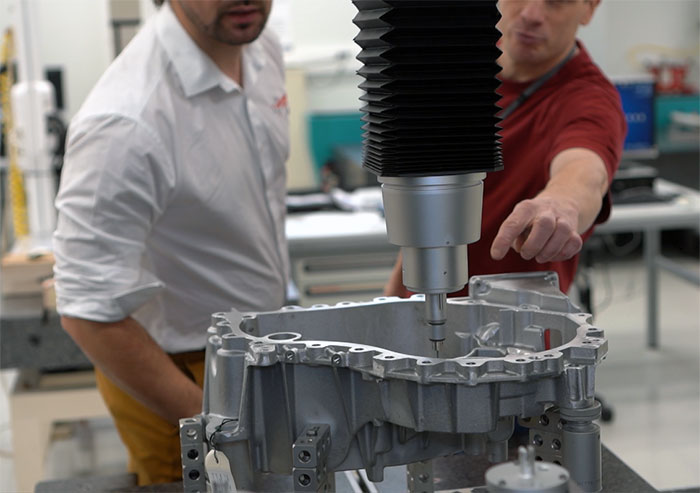
This retrofit project carried out for the Stellantis technical center is a fine demonstration of the technical support Metrologic Group can offer its customers. By choosing Metrolog X4, Stellantis has not only modernized its measuring equipment, but also optimized the performance and durability of its CMMs, while keeping costs under control.
“Thanks to Metrologic Group’s expertise and everyone’s commitment, we now have high-performance, long-lasting measuring tools that are perfectly suited to the demands of our business”, says Jean-Pierre HUGUET.
This success is based on genuine collaboration between the teams, reinforced by almost 30 years of partnership and a relationship of trust based on responsiveness, ongoing support and solutions adapted to Stellantis’ changing needs. “A big thank you to Stellantis, for their trust and loyalty. It’s a real source of pride to work together on this kind of project,” concludes Etienne COIFFARD, Strategic Key Account Manager at Metrologic Group.
At Metrologic Group, we are proud to support our customers in their technical challenges by offering them comprehensive services, from retrofit to maintenance, including tailored training. Drawing on our 40 years of expertise in industrial metrology, we remain at our customers’ side to extend the life of their CMMs and support their activities over the long term.
What’s next at Stellantis?
Thanks to this investment in Metrolog X4, Stellantis is currently planning to centralize the roughness and gear measurement functions on a single machine, and therefore on a single software package. Renishaw’s REVO 5-axis measuring head complements Metrolog X4 perfectly.
Today, these applications are carried out using dedicated software and machines, making implementation more complex.
The next step for Stellantis is to take advantage of the universality of Metrologic Group solutions to boost performance.
Many thanks to José FERNANDEZ for his trust and loyalty
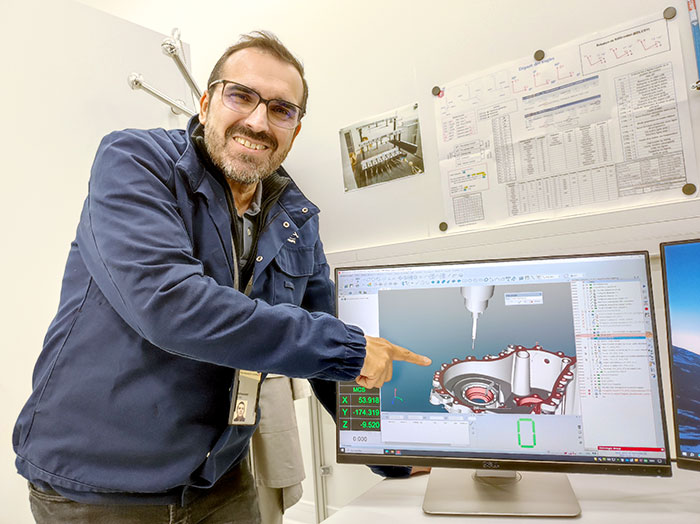
As 3D support technician, José FERNANDEZ is responsible for Metrolog X4 measurements at the Stellantis site. He also plays a cross-functional and global role within the Stellantis group for mechanical parts. As part of his job, he is responsible for testing new modules and monitoring technology to improve processes.
This is why he is the initiator of this retrofit project. The smooth running of Metrolog X4 on this machine was validated by working with Kevin SOUVIGNET, his dedicated technical application engineer at Metrologic Group. José FERNANDEZ was also involved in the development and continuous improvement of our product.
Many thanks for his availability, transparency and dedication, as well as to the whole team who welcomed us with the same enthusiasm.
About Stellantis
With industrial activities in over 30 countries and customers in more than 130 markets, Stellantis brings together the world’s most emblematic automotive brands: 14 automotive brands and 2 brands dedicated to mobility. Thanks to cutting-edge technologies at the heart of its products and services, Stellantis is at the forefront of electrification and software development.
Focused on its customers and supported by partners who are leaders in their sectors, Stellantis aims to develop, design, manufacture and offer the best for every aspect of sustainable mobility: autonomous driving, connected vehicles, electrified cars, shared mobility, used vehicles, micromobility, utilities and even electric aircraft.
The Carrières-sous-Poissy technical center is located on the right bank of the Seine, opposite the Poissy plant and Expertise Center in the Paris region (France). Together with the Poissy site and the Vélizy site, this is one of three Stellantis sites in the Yvelines.